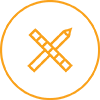
DESIGN AND DEVELOPMENT
We support our customers in the process of cast design. When designing moulds and pressure casting support tools, we work using CAD/CAM software such as NX/Siemens, CREO, and VERICUT. Our equipment resources include a FARO measuring arm with a scanning head and Cam 2 measure software, which makes it possible to create a model on the basis of an existing (scanned) item.
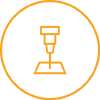
MOULD CONSTRUCTION
Our modern equipment resources include:
- Milling machine DMU 125 monoBLOCK (5 axes)
- Vertical machining centre DMG 1035
- Vertical machining centre DMU 60
- CNC milling machine MAHO (7 units)
- High-speed milling machine Mikron Mill S 500 (for graphite electrode machining)
- Deep hole drilling machine DEGEN
- Wire-cut EDM (electrical discharge machine) Fanuc Robocut C800iB
- Wire-cut EDM (electrical discharge machine) Charmilles Robofill 690
- Sinker EDM (electrical discharge machine) AgieCharmilles FORM 30
- 3-chamber ultrasonic cleaning system for molds FISA
Our equipment lets us form molds of the weight of up to 10 tons.
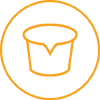
DIE CASTING
Aluminium, obtained in an energy-efficient manner, is melted in a shaft furnace with an automatic weight measurement system. We have 11 real-time controlled casting machines at our disposal, operating at a closing force of 450t to 1350t. All of our machines are equipped with automatic pouring cups, and some feature robotic sprinklers. Process automation and control of each stage thereof ensure great stability of the casting process.
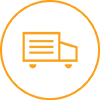
LOGISTICS
Our customers receive ready products. We use reusable packaging.